Un peu d’histoire… pour bien comprendre le contexte
Le JIPM, pour Japan Institute of Plant Maintenance a été créé en 1981 sur les bases du Plant Maintenance Commitee fondé en 1961 par le JMA Japan Management Association.
Il s’agit de la collaboration d’industriels japonais désireux de mettre en commun leur expérience de la maintenance dans leurs usines.
C’est le désormais illustre JIPM qui a bâti le concept de TPM pour TOTAL PRODUCTIVE MAINTENANCE.
Plant Maintenance, Productive Maintenance, Planned Maintenance, Predictive Maintenance… autant de possibilité pour PM, pourtant ce que je me propose d’éclaircir ici n’est aucun de ces termes ci-dessus, bien que ce soit lié à tous.
ANALYSE PM est un élément précis de la TPM qui est un système de management de la maintenance dont le but ultime est de garantir le bon fonctionnement des équipements au moment où on en a besoin, et par extension de réduire les coûts globaux de maintenance. Ce système inclut la qualité de production, la disponibilité des moyens, la formation des hommes, l’ergonomie lors de la maintenance, la réduction des pertes, le respect de l’environnement etc… (d’où le nom de TPM TRUE PEOPLE qui vous propose une démarche globale).
On propose souvent d’expliquer ou d’appliquer la TPM au travers de « piliers ». Je n’ai personnellement pas trouvé le terme de « pillar » dans les documents du JIPM, mais soit, il y a des grands sujets, reliés entre eux, et aucun ne fonctionne tout seul. Parmi ces sujets, les indicateurs (cf article sur l’OEE/ TRS), l’élimination des pertes, la Maintenance Autonome, la Maintenance Planifiée ou Programmée, dont la Maintenance Prédictive, et la conception des nouveaux équipements qui tente d’appliquer, en amont de l’achat, l’expérience de la TPM acquise par l’entreprise. La sécurité, la formation, la qualité, l’ergonomie la standardisation, les chantiers Kaizen et l’informatisation sont des notions transversales à tous ces sujets.
L’analyse PM est une méthode d’analyse poussée qui est utile là où les méthodes de résolution de problème conventionnelles ne suffisent pas.
P signifie Phénomène et Physique
M pour Mécanisme et pour les 4 M d’Ishikawa : l’arbre des causes ou encore Fishbone tree.
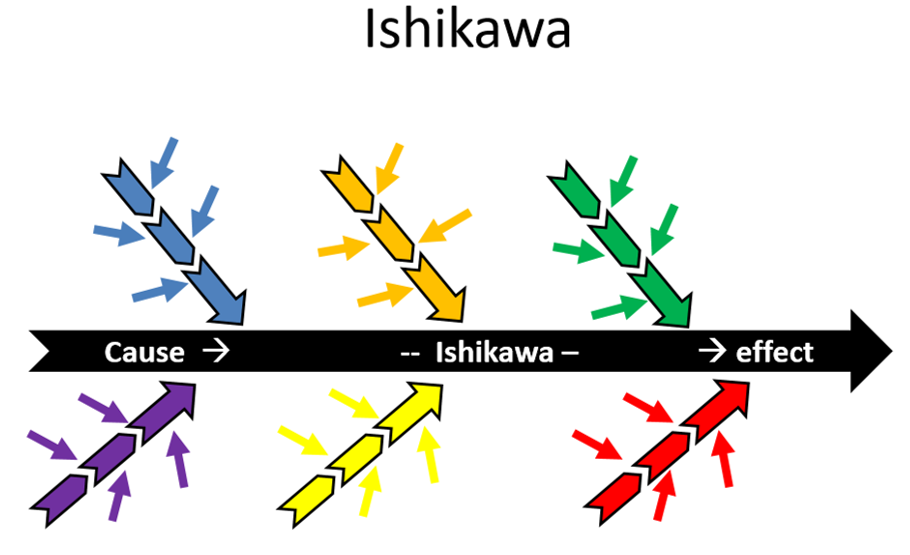
Pour mémoire, les 4M en question sont Machine, Matière, huMain, et Méthode, auquels on peut ajouter Management, Moyens de Mesure.
Le JIPM propose huit étapes pour l’analyse PM :
- Clarifier le problème (en regardant les faits réels, sur le terrain, pas dans les bouquins)
- Rechercher, mesurer, analyser les principes physiques qui sont impliqués. Comment le problème survient-il ?
- Identifier les conditions dans lesquels le problème survient.
- Considérer la relation entre les conditions des étapes précédentes et les intrants de production (les 4M). Il s’agit d’aller chercher les phénomènes physiques de manière scientifique. Le piège serait de sauter sur la première cause venue pour lui attribuer la responsabilité du phénomène. Aucun facteur ne doit être écarté à la légère !
- Déterminer les conditions optimales.
- Déterminer la meilleure méthode de mesure pour « monitorer » le phénomène.
- Identifier les déficiences de chaque facteur.
- Formuler et mettre en place un plan d’action d’amélioration.
Avec les moyens modernes de digitalisation, on peut plus précisément représenter et même mesurer les phénomènes que dans les années 80. Néanmoins, l’esprit et les principes demeurent. Un beau schéma 3D ne remplace pas les cerveaux qui cogitent et considèrent la réalité du terrain.
Vous l’avez sans doute perçu, nous parlons d’une approche qui est celle de la Maintenance Prédictive. Une approche scientifique détaillée pour connaitre à fond le fonctionnement d’un équipement.
Ainsi, partant d’un problème que le management aura d’abord traité selon les standards de résolution de problème, on découvre qu’on doit aller plus loin pour garantir à chaque fois le bon niveau d’exigence qualité et de fiabilité.

Dans TPM in Process Industries, Tokutaro Suzuki insiste sur le fait que l’analyse PM intervient dans les cas avancés de maintenance. Si votre taux de panne excède 0,5%, vous avez d’autres priorités que la maintenance prédictive et il vous faut revenir au sujets fondamentaux de la TPM.
TRUE PEOPLE est là pour vous accompagner sur la voie de l’excellence par la maîtrise de vos processus.