S’il est un indicateur à suivre pour piloter la performance c’est le TRS. (Taux de Rendement Synthétique), en anglais OEE (Overall Equipment Efficiency).
Comme tout outil efficace, si on l’utilise mal il peut néanmoins faire plus de dégâts que de bien.
En effet, si je rencontre encore régulièrement des PME qui ne mesurent pas le TRS, je vois trop souvent des gens qui en utilisent mal le résultat, ou se trompent de finalité ou de périmètre.
Je vous propose dans un premier temps de clarifier la définition du TRS par rapport au TRG (Taux de Rendement Global) et au TRE (Taux de Rendement Economique), puis parmi ces options, comment choisir l’indicateur adapté. Je finirai avec une considération managériale sur le risque réel de détruire les intérêts du TRS.
Les termes et définitions de cet exposé sont conformes à la norme NFE 60-182 qui précise le vocabulaire et le mode de calcul du TRS
- Qu’est-ce que le TRS ?
Le TRS est le ratio entre le temps réellement utilisé à produire des pièces bonnes et le temps opérationnel (temps prévu de production).
NB : je dis pièce par facilité d’expression mais il peut s’agir d’un produit ou d’un service.
Qu’est que le temps opérationnel ? Dans l’activité d’une entreprise, on distingue trois types de temps : le temps total, le temps d’ouverture, et le temps opérationnel qui apparaissent clairement sur le schéma ci-dessous.
Le temps total est 24/24h, 365 jours /an. Seules certaines activités, qui ne ferment jamais, sont concernées. Le TRE est calculé sur ce temps total.
Le temps d’ouverture est celui où l’atelier est ouvert.
Le TRG est calculé sur ce temps d’ouverture (y compris la maintenance planifiée, les pauses, réunions prévues etc…).
Le temps opérationnel est le temps pendant lequel on a décidé de produire des pièces.
C’est sur ce temps que se base le TRS.
Tout ce qui est soustrait à ce temps opérationnel est donc considéré comme perte, puisque non prévu, et à éliminer.
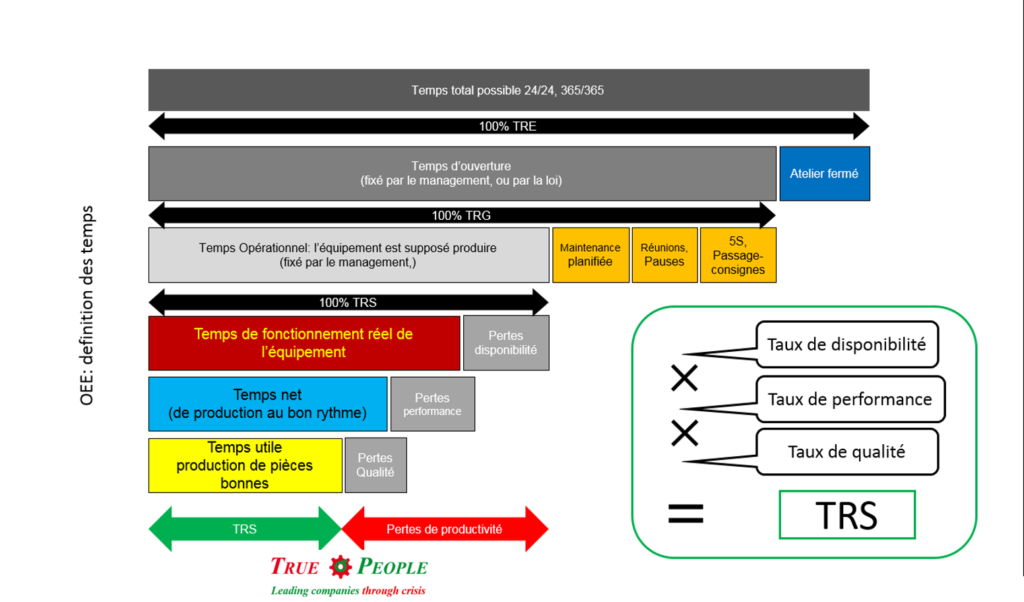
Il y a trois grandes catégories de pertes : Disponibilité (l’équipement produit ou pas), Performance (l’équipement produit, mais plus lentement que prévu) et Qualité (il y a des pièces non-conformes).
Je rentrerai dans le détail de l’analyse et des pertes et leur élimination dans un article ultérieur.
Le TRS peut s’exprimer en temps ou en pièces :
Temps utile de production de pièces bonnes au rythme prévu sur le temps de production prévu . Pour l’activité d’un Taxi, par exemple, le temps de production utile serait celui pendant lequel un client est à bord, et donc facturé. Si ce temps est de 7 h par jour, sur un temps de conduite prévu de 9 h, son TRS est de 7h/9h.
Dès lors que vous produisez des pièces, je trouve plus parlant d’exprimer votre efficience en nombre de pièces. J’ai fabriqué 40 pièces au lieu de 70 prévues, pendant le temps opérationnel.
2. Pourquoi choisir le TRS comme indicateur ?
Le premier critère est votre temps d’ouverture. Si l’atelier est ouvert 8 heures par jour et fermé pendant les vacances, il n’y a aucun intérêt à mesurer le TRE (24/24 et 365 jours /an)
Le deuxième critère relève de la volonté du management :
En optant pour le calcul du TRG qui considère tout le temps où l’atelier est ouvert comme disponible, (donc temps d’ouverture), on montre qu’il y a une marge de manœuvre pour augmenter le temps opérationnel si nécessaire.
Par exemple, si votre équipement est goulot et que vous ne pouvez pas suivre la demande client, avant de décider d’investir dans un nouvel équipement supplémentaire, la question de l’augmentation du temps de fonctionnement du poste et de son équipement va se poser. Je ne dis pas que ce sera la bonne option, mais je dis qu’il faut garder à l’esprit que le poste n’est pas chargé à 100%.
Avant tout, et grâce aux principes de la TPM, on rendra l’équipement suffisamment fiable pour éliminer les pertes.
Le risque de mesurer le TRG, en revanche, c’est de considérer que le temps réservé à l’entretien de l’équipement ou à son amélioration peut être rogné sans limite, et ainsi de s’exposer à des pannes, de la non-qualité, voire des accidents.
Par ailleurs, si vous communiquez avec le TRG, vous aurez du mal à empêcher que les opérateurs ne veuillent tendre vers 100% et que, au final, des retards accumulés sur le temps opérationnel ne soient récupérés sur les temps d’arrêt planifiés. Votre mesure devient erronée.
Il faut une grande maturité dans la culture de l’entreprise pour utiliser le TRG sans ces risques.
Avant d’être capable de réduire les temps de maintenance planifiée, les temps de remise en condition de l’équipement entre chaque poste (5S et passage de consignes), cela suppose que votre niveau de maturité TPM soit déjà très bon : Zéro panne, Zéro défaut, Zéro accident, strictement.
Par conséquent, je conseille de commencer par ne mesurer que le TRS, en tout cas sur le terrain.
3. Pourquoi le calcul du TRS peut devenir un danger ?
Première remarque : Le Taux de Rendement Synthétique est un indicateur. Ce n’est pas un objectif.
Le TRS indique s’il y a des problèmes et où il y a des problèmes, lesquels, et combien.
Dans le précédent paragraphe j’évoquais la tendance des opérateurs à tendre vers 100%, cela devient très certain si vous leur fixez un objectif de maximisation du TRS. Nous sommes dressés depuis l’école maternelle à avoir de bonnes notes. Fixez un objectif que vous jugez raisonnable, par exemple 80%. Vous l’obtiendrez probablement. Aurez-vous, pour autant, éliminé les arrêts non prévus, les baisses de régime, les défauts… ? Nenni ! Ils sont cachés, dissimulés. Vous vouliez des chiffres, des notes, vous les avez.
Le TRS n’est pas un objectif, c’est un révélateur de problèmes. Vous devez résoudre ces problèmes, et non rajouter un poids sur les épaules des utilisateurs. Les opérateurs doivent montrer ce qui ne va pas. Si vous les jugez inefficients quand il y a un problème, il n’y aura plus de problème. C’est le coucours d’autruche!

Le TRS n’est donc pas un objectif en soi, c’est l’élimination des pertes qui est l’objectif.
La mesure séparée du taux de disponibilité, pour commencer, va mettre en écart la réalité avec le but qui est que l’équipement ne s’arrête pas sur la durée du temps opérationnel.
Si le taux n’est pas de 100%, c’est donc que la machine s’est arrêtée. Est-ce que l’opérateur y peut quelque chose ? Presque toujours non. Il a pu manquer de matière en amont, le système n’a pas prévu un remplaçant pour la réunion exceptionnelle, il y a eu une panne parce que la maintenance préventive a encore été reportée… Quel message envoyez-vous à l’opérateur en exigeant un objectif de TRS dans ces conditions?
Taux de Qualité : Idem.
Taux de performance, à observer de plus près…en général c’est aussi dû à des failles du système et non de l’opérateur.
Je vous renvoie à mon article sur les causes communes vs causes spéciales.
Deuxième remarque : Le TRS doit être calculé pour chaque équipement individuellement, et non pas globalement pour la ligne, l’ilot, voire l’atelier. Ça n’a pas de sens, un TRS atelier. Quel est le problème ? C’est tel équipement de tel atelier.
Pour conclure, le TRS est indispensable pour percevoir les pertes d’un équipement ou d’un poste.
Une fois les pertes identifiées, on peut s’atteler à en éliminer les causes racines.
C’est l’occasion, pour le management de venir en soutien au terrain par les méthodes de résolution de problème, et de faire progresser ensemble, chaque jour un peu plus l’entreprise vers l’excellence.
Le processus TPM est un chemin long et difficile mais passionnant. S’il est apparu d’abord dans l’industrie, ses principes peuvent s’appliquer dès lors que vous dépendez d’un équipement pour travailler.
J’encourage les patrons de PME à se pencher sérieusement sur la question et à inviter des yeux nouveaux dans leur atelier. Il y a sans aucun doute de nombreuses opportunités de progrès à découvrir.
N’hésitez pas à me contacter.
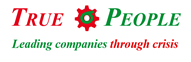
Thierry BLANCHAT